Milling inMadison Heights, MI
Expert Asphalt Milling for a Flawless Repaving Process
We Are Locally Owned & Operated For Over 37 Years
Contact Us Today!
We Serve Businesses In And Around The Following Cities:
About Milling
Introduction
In the dynamic landscape of commercial property development and maintenance in Madison Heights, milling has emerged as an essential process that transforms aging surfaces into renewed assets. The technique is particularly valuable for commercial properties where smooth, durable surfaces are integral not only for aesthetic appeal but also for efficient operations and safety. Milling in Madison Heights for commercial properties involves the systematic removal of a worn-out asphalt layer to expose a fresh layer underneath, setting the stage for a variety of applications ranging from parking lot rehabilitation to roadway maintenance. As businesses grow and traffic demands increase, property owners find that investing in milling methods pays off by extending the life of their surfaces while reducing further structural degradation and maintenance costs. This article provides a deep dive into the milling process, discussing its benefits, the nuanced aspects of its application, and real-world examples that illustrate how milling can rejuvenate commercial properties in Madison Heights.
Historically, milling has been associated with roadway reconstruction and repair. However, contemporary advancements have broadened its scope, enabling milling contractors to apply innovative techniques that cater to a wide range of commercial and industrial settings. This evolution has been fueled in part by the integration of modern machinery and technologies that allow for more precise and efficient milling. The result is a process that not only enhances operational safety for vehicles and pedestrians but also maximizes the lifespan of the surface material. In recent times, local stakeholders, including property managers and municipal officials, have increasingly recognized the significance of milling in preserving high-traffic areas, making it an indispensable tool in urban infrastructure management.
Commercial properties in Madison Heights benefit from milling in several ways. The process effectively removes imperfections and wear that have accumulated over time, contributing to hazards and deterioration. In parking lots, for example, thorough milling clears out the surface irregularities, ensuring a flat, reliable base for new asphalt overlay or resurfacing. Integration of milling has also enabled businesses to address underlying issues related to drainage and structural integrity. By exposing the sound layers beneath the damaged top asphalt, contractors can better assess the condition of the base and implement corrections before applying a new surface. This preventative maintenance not only enhances the performance of the entire structure but also significantly reduces long-term repair costs.
The journey of understanding milling begins with recognizing the challenges associated with deteriorating asphalt surfaces. Constant exposure to weather extremes, heavy vehicular loads, and time invariably leads to the formation of cracks, potholes, and depressions. Relying solely on patchwork repairs is no longer sufficient; instead, a more robust solution in the form of asphalt milling is required. The process involves using state-of-the-art equipment that grinds away the compromised layers, thereby restoring the surface to a state that is optimal for resurfacing. This technical procedure not only revitalizes the appearance of commercial premises but also reinforces the structural reliability of the entire area.
Furthermore, as local businesses strive to stay competitive and adhere to evolving regulations, milling has garnered increased attention for its sustainable and cost-effective merits. With the integration of recycled materials, modern milling techniques promote eco-friendly practices, reducing waste and leading to a circular utilization of resources. This aspect resonates particularly well with community-focused initiatives in Madison Heights that aim to balance developmental progress with environmental stewardship. In this context, milling is not just a repair technique—it is a strategic investment in a commercial property’s longevity and marketability.
Understanding the Milling Process
At its core, the milling process is a carefully calibrated method designed to remove a designated depth of asphalt from a paved surface. This procedure is often employed on parking lots, highways, and other high-traffic commercial areas where degradation is common. The milling process starts by assessing the area to establish the required depth of removal. Once these parameters are defined, a milling machine—a piece of heavy-duty equipment equipped with rotating drums embedded with carbide cutters—begins to grind away the old, distressed top layer. This can be done uniformly to ensure consistency in the worn surface or selectively, depending on the specific needs of the area.
The milling procedure is particularly beneficial because it addresses multiple problems in a single operation. Firstly, it eliminates surfaces that have been compromised due to weathering and repeated use, including factors like water infiltration and freeze-thaw cycles. Secondly, by removing uneven layers or damaged sections, milling presents the underlying base in its best possible condition. This allows subsequent layers to bond more effectively, ultimately providing a smoother, more resilient finish. The entire process is a blend of precision and power, emphasizing both technical expertise and the quality of the equipment used.
Modern techniques such as asphalt cold milling further enhance this process by offering environmentally friendly options that minimize the energy consumption typically associated with heated milling methods. Asphalt cold milling uses advanced technology to achieve high performance without the environmental drawbacks of traditional hot milling methods. This evolution in technology demonstrates how milling in Madison Heights has progressed to meet higher standards of efficiency and sustainability. Local asphalt milling companies have embraced these advancements, providing their commercial clients with improved service quality and cost savings over time.
In addition to the technical aspects, the planning and implementation phases are equally crucial in the success of a milling project. A detailed assessment of the commercial property’s layout, traffic patterns, and existing pavement conditions is essential. From this comprehensive evaluation, milling contractors can develop a bespoke strategy tailored to each unique project. By carefully synchronizing machinery operations with on-site logistics, they ensure minimal disruption to business operations. This meticulous approach not only underscores the importance of an experienced milling contractor but also confirms why many businesses in Madison Heights trust in seasoned professionals when it comes to preserving and rejuvenating commercial surfaces.
Benefits for Commercial Properties
The advantages of milling extend far beyond the immediate restoration of worn surfaces. For commercial properties in Madison Heights, the process of asphalt milling represents a viable long-term investment that circumvents the need for frequent repairs. One of the most significant benefits is the enhancement of overall surface quality. When damaged asphalt is removed, the resulting surface is smooth and uniform, which aids in mitigating the risks of accidents and other hazards that often arise due to cracks or uneven terrain. Additionally, a well-milled surface is far more aesthetically pleasing, which in turn elevates the property’s overall image and can influence customer perception.
Business owners who prioritize safety and functionality find that milling offers tangible economic benefits. For instance, in parking lots where consistent wear and tear is expected, regular milling and timely resurfacing can extend the lifespan of the pavement dramatically. This proactive approach helps in preventing more severe damage that might otherwise require costly, large-scale reconstructions. Asphalt milling services provided by local contractors, including asphalt parking lot milling options, are designed to be both efficient and minimally disruptive. By scheduling work during off-peak hours, businesses can maintain operations without compromise, ensuring that the commercial property continues to be a safe environment for customers, employees, and visitors alike.
In addition to preserving and rehabilitating surfaces, the milling process has environmental benefits. By removing and reusing the existing asphalt layer, local recycling practices are encouraged, reducing material wastage and promoting sustainability. Asphalt milling companies advocate for the reuse of milled material in new overlays or even in structural components of newer pavement layers. This not only saves on materials but also contributes to a decrease in the overall carbon footprint associated with demolition and repaving projects. Moreover, reference to incentives available in Madison Heights for sustainable practices further emphasizes the importance of adopting milling techniques that are both economically and ecologically sound.
Property managers and facility owners also benefit from the increased safety that results from effective milling. The smooth surfaces that come out of a well-executed milling operation provide better traction for vehicles and prevent the collection of water in depressions that can lead to hydroplaning or flooding during heavy rains. By addressing potential hazards preemptively, milling plays a critical role in protecting both property and public welfare. These risk mitigation measures are particularly significant in high-traffic areas like shopping centers, office complexes, and industrial parks where the margin for error is exceptionally low.
Process Details of Asphalt Milling
Delving into the specifics of asphalt milling, one finds that the process is a well-orchestrated interplay between advanced machinery and skilled technicians. The machinery used in this process is capable of removing layers of asphalt with precision and efficiency. Asphalt milling contractors rely on equipment that is designed to operate under various conditions, including different types of asphalt surfaces and weather situations. Whether dealing with densely paved commercial lots or expansive roadways, these machines are engineered to cope with the challenges presented by thick, old layers of asphalt.
One key approach in achieving optimal results is the practice of asphalt cold milling. This modern technique allows for milling without the excessive heat that can sometimes compromise the quality of the underlying base. By performing milling at lower temperatures, asphalt cold milling helps maintain the integrity of the base material, which is crucial for ensuring a long-lasting new overlay. This method is particularly effective in areas where temperature fluctuations are common, safeguarding against premature deterioration caused by thermal stress. Such advancements have also led to the emergence of specialized asphalt milling services that cater to niche requirements—ranging from minor repairs to extensive surface overhauls.
The workflow typically begins with a detailed survey of the area. Measurements are taken, and the extent of the damage is documented, allowing the milling contractor to develop a tailored plan for the project. Once the project parameters are set, the milling machine engages with the asphalt surface. The high-speed rotating drum, fitted with cutting teeth, shaves off the top layer layer by layer. This operation is both meticulous and efficient, ensuring that only the necessary depth is removed. In doing so, the machine preserves portions of the asphalt that remain structurally sound, thereby reducing waste.
Throughout the milling process, constant monitoring ensures that the operation adheres to safety protocols and quality standards. The aim is not only to remove deteriorated material but also to prepare the surface for a new, more resilient coat of asphalt. Moreover, many asphalt milling companies have integrated advanced monitoring systems that track the progress of the milling operation in real time. This is critical for adjusting the process on the fly and for ensuring that the final surface meets the stringent standards expected in commercial applications.
Environmental factors also play a role in the overall success of asphalt milling operations. For instance, proper drainage and surface permeability are key aspects that need restoration during milling. By removing the upper, worn-out asphalt layer, contractors can better address issues such as pooling water and compromised drainage systems. This aspect is particularly valuable in commercial districts like Madison Heights where weather conditions can greatly affect the usability of parking lots and roadways. Whether addressing safety concerns or preventive maintenance, every step of the milling process contributes to enhancing the property’s overall durability.
Real World Applications in Madison Heights
Madison Heights, with its blend of residential charm and commercial growth, offers a unique backdrop for showcasing the real-world applications of milling. In this vibrant city, commercial properties such as shopping centers, office parks, and industrial facilities have reaped significant benefits from adopting milling as a core maintenance strategy. Local businesses have noticed remarkable improvements in safety, durability, and overall cost efficiency by integrating milling into their property care routines. Every project tells a story of how traditional asphalt surfaces, once marred by years of wear and tear, can be transformed into durable canvases ready for future use.
A practical example can be seen in the rehabilitation of parking lots that have served as key arteries for commercial activity. Over time, these surfaces begin to show signs of heavy wear—cracks, depressions, and general degradation become common. Instead of embarking on a full-scale reconstruction, many property managers opt for parking lot milling. This process removes only the compromised top layer, leaving behind a solid base that is perfect for resurfacing with new, high-performance asphalt. Such maintenance not only restores functionality but also significantly enhances the visual appeal of the space, contributing to a positive customer experience.
Several local asphalt milling companies near me have earned stellar reputations by successfully executing projects that involve parking lot milling and asphalt cold milling. These firms leverage their deep understanding of local conditions—be it the typical weather patterns or traffic densities—to deliver tailored solutions that meet the highest quality standards. Their expertise has proven especially beneficial in commercial contexts where time is of the essence and disruptions must be minimized. Many businesses have turned to trusted milling contractors to ensure that their properties remain operational even during maintenance. In such cases, operations are carefully planned during off-peak hours, and advanced equipment is employed to complete the projects swiftly and effectively.
Beyond parking lots, the milling process has also been applied to larger-scale roadway improvements in Madison Heights. For instance, commercial corridors that experience heavy vehicular traffic undergo regular milling to keep road surfaces safe and drip-free. Municipalities and private entities alike have recognized the strategic value of preventive milling in maintaining smooth pavement conditions and prolonging the life of their infrastructure. In these applications, milling is seen as a cost-effective and forward-thinking approach that reduces the need for more extensive rehabilitation later on. The effective deployment of such techniques has made a noticeable difference in the overall quality of Madison Heights’ commercial infrastructure.
Furthermore, some commercial property owners have engaged in adaptive reuse projects where milling plays an integral role. In situations where older commercial centers are being reimagined for new purposes, milling offers a practical way to prepare existing surfaces for modern overlays. This method not only preserves historical elements of the architecture but also adapts them to contemporary needs with minimal environmental impact. As businesses continue to innovate in their use of space, the milling process stands out as a versatile solution that seamlessly bridges the gap between the old and the new.
Customizing Milling for Business Needs
One of the most appealing aspects of milling for commercial properties is its inherent flexibility in customization. No two commercial properties are entirely alike; each has its own set of challenges, be it varying levels of wear, unique traffic patterns, or differing structural conditions. Recognizing these variables, milling operations can be tailored specifically to address the distinct needs of each project. For example, a commercial parking facility that experiences high volumes of heavy vehicles may require deeper milling to remove all compromised materials and ensure the remaining base can support future loading demands. Conversely, a lightly used outdoor mall walkway might only necessitate superficial milling to restore its evenness and functionality.
Property managers in Madison Heights often collaborate closely with experienced asphalt milling contractors to develop a customized plan that aligns with both the immediate repair needs and long-term strategic goals of their projects. Detailed site assessments and consultations allow for precise measurements and recommendations regarding the scope of milling required. Through this collaborative process, local experts can advise on the optimal balance between cost, time efficiency, and the durability of the final product.
In addition to structural improvements, customized milling also opens the door to incorporating innovative materials and techniques. Several asphalt milling companies have integrated recycled materials into their processes, thereby reducing costs and advancing sustainability objectives. For instance, reclaimed asphalt pavement (RAP) from a milling project can be processed and reused in new overlays, which not only keeps upkeep expenses lower but also aligns with environmentally conscious practices. Such sustainable approaches have gained traction among commercial property owners who are committed to reducing their carbon footprint.
The adaptability of milling further extends to its compatibility with other maintenance practices. In many instances, milling serves as a preparatory step that enables the successful application of a new surface treatment. Whether it is a specialized anti-slip overlay for a commercial garden center or an enhanced drainage system for a busy retail parking lot, the milling process forms the critical foundation upon which these additional enhancements are built. This integrative approach ensures that every layer added to the property works in harmony to produce a surface that is both resilient and aesthetically pleasing.
In the context of Madison Heights, local businesses have reported substantial improvements in operational efficiency and customer satisfaction following customized milling projects. The process not only renews the appearance of the surface but also instills a sense of security and reliability among users. As the city continues to flourish, the capacity to tailor milling services to specific business needs underscores the strategic importance of choosing a dependable milling contractor who understands the local landscape and the unique requirements of commercial properties.
Economics and Sustainability in Milling
Economic considerations play a pivotal role in the decision-making process for commercial property owners, and milling offers considerable advantages from an investment standpoint. The milling process is often more cost-effective than completely replacing an asphalt surface because it focuses on rejuvenating rather than demolishing. This approach minimizes waste, lowers labor costs, and reduces the time required to get a project back on track. For many commercial properties in Madison Heights, these factors translate into reduced operational costs and enhanced asset longevity, making milling not just a repair solution but a strategic financial decision.
Sustainability is another key factor that underscores the benefits of milling. When asphalt is milled correctly, the reclaimed material can be reprocessed and repurposed to create new overlays. This recycling initiative supports eco-friendly practices, reducing the need to source entirely new materials and lowering overall environmental impact. The industry’s move towards sustainability has also led to improved technologies and methodologies, such as asphalt cold milling, which further minimize energy consumption during the milling process. These practices have made it possible for commercial property owners to achieve a balance between economic efficiency and environmental responsibility.
The recycling aspect of milling is particularly influential in today’s market, where businesses are increasingly judged by their ability to adopt green practices. In Madison Heights, where community and environmental responsibility are highly valued, the ability to reduce carbon footprints through sustainable maintenance practices has become a significant selling point. Local asphalt milling companies have adopted these eco-friendly methods, demonstrating that effective pavement rehabilitation and environmental conservation can go hand in hand.
Financially, the benefits of milling extend beyond immediate cost savings. Studies have shown that properties maintained with regular milling and resurfacing schedules tend to have higher market values than those where maintenance efforts are sporadic or reactive. The proactive approach of addressing minor surface issues before they become significant problems not only protects the structural integrity of the property but also preserves its long-term market appeal. This forward-thinking strategy is particularly beneficial in a growing urban area like Madison Heights, where competing commercial properties continuously seek to enhance their operational efficiency and curb appeal.
Moreover, the integration of advanced machinery and precision techniques has contributed to improving the overall ROI (Return on Investment) for milling projects. The combination of cost-effective maintenance methods and the potential for material recycling enhances the economic feasibility of such projects. By selecting expert milling contractors who are well versed in modern technologies and environmentally sustainable practices, commercial property owners can ensure that every dollar spent on maintenance is an investment towards a longer-lasting, safer, and more attractive surface.
Maintenance and Long Term Benefits
Regular maintenance is paramount to prolonging the lifespan of asphalt surfaces, and milling plays a critical role in this preventative strategy. For commercial properties in Madison Heights, consistent and methodical asphalt milling can catch early signs of wear before they develop into more extensive structural problems. This preventive measure not only reduces emergency repair costs but also minimizes the business disruptions that occur when sizable repair projects are initiated unexpectedly. By maintaining a regular milling schedule, property owners ensure that their surfaces remain functional and aesthetically pleasing, even as vehicles and foot traffic continue to take their toll.
The long-term benefits of milling are manifold. One significant advantage is the enhanced bonding that results when a new asphalt layer is applied over a properly milled surface. This improved adhesion reduces the risk of future delamination, cracking, or water infiltration, thereby preserving the quality of the pavement over time. Businesses that routinely invest in milling as part of their maintenance protocol report extended surface life, leading to increased durability and a lower overall cost of ownership. In addition to these performance advantages, the regular upkeep of asphalt surfaces contributes positively to the overall safety and operational efficiency of commercial spaces.
Another noteworthy benefit is the mitigation of hazards that could arise from an uneven or deteriorated surface. Commercial properties where parking lot milling has been effectively executed witness a marked reduction in accidents caused by potholes and uneven surfaces. In busy commercial districts, such as those in Madison Heights, the ability to provide smooth and reliable pavement is paramount to ensuring that property users—whether customers, employees, or delivery vehicles—experience a safe environment. The improved surface conditions also translate into fewer liability issues and a more positive perception of the property by the public.
Regular milling aligns with the philosophy of preventive maintenance, which is particularly crucial in environments where extended downtimes can result in significant financial losses. Asphalt milling contractors typically offer routine inspections as part of their service packages, ensuring that any emerging issues are promptly addressed. This proactive approach enables faster turnaround times whenever repairs are needed and reduces the likelihood of unexpected failures. Over time, commercial property owners can see measurable cost savings and enhanced asset longevity by incorporating systematic milling into their long-term maintenance plans.
In addition, modern milling techniques often incorporate technologically advanced diagnostic tools. These tools help identify specific problem areas that may require targeted solutions, further optimizing the maintenance process. The ability to precisely assess and address localized wear means that resources can be allocated more efficiently, enhancing the overall effectiveness of the maintenance strategy. By trusting experienced milling contractors and utilizing contemporary milling practices, commercial properties in Madison Heights can enjoy a level of pavement integrity that supports ongoing business activities and enhances property values.
Choosing the Right Milling Contractor
Selecting the right milling contractor is crucial to the overall success of any milling project. The complexity of asphalt milling, along with the need for precision and efficiency, demands a contractor with a proven track record, robust equipment, and a deep understanding of local market requirements in Madison Heights. Prospective clients should seek out asphalt milling contractors who have demonstrated expertise in a variety of applications, whether it is asphalt cold milling or meticulous parking lot milling. Experienced professionals are better positioned to provide tailored solutions that accommodate the specific challenges and conditions of each commercial property.
When evaluating potential contractors, property owners will benefit from considering customer testimonials, project portfolios, and the quality of the machinery used. Many businesses search for terms such as “asphalt milling companies near me” or “asphalt milling services” to identify local experts who can deliver timely and effective results. It is equally important to engage with contractors who are committed not only to technical excellence but also to high standards of safety and environmental responsibility. In a city like Madison Heights, where local reputation and community trust matter, selecting professionals who clearly embody these qualities is essential.
A notable example of a reliable milling service provider in the area is D&J Contracting, a company known for its dedication to quality and efficiency. While many asphalt milling companies offer similar services, working with a contractor who has a well-established reputation in the community can make a significant difference, particularly during time-sensitive projects. The recommendations of local businesses and property owners reinforce the importance of choosing a contractor who not only excels technically but also understands the local climate, soil conditions, and traffic patterns that influence the milling process.
In addition to technical competence, clear communication and a customer-focused approach are hallmarks of an outstanding milling contractor. The complexity of planning and executing a milling project necessitates that property owners stay informed at every stage, from initial inspection to final resurfacing. Contractors who take the time to explain the specifics of the milling process and customize their approach based on individual property characteristics can provide clients with the assurance that their investment is well-placed. With the right partner, businesses can strategically plan their maintenance schedules, striking a balance between operational continuity and the necessary infrastructure upgrades.
Ultimately, the decision to engage with a milling contractor should be seen as a strategic investment in the long-term durability and performance of a commercial property. Whether the project entails extensive roadway rehabilitation or concentrated asphalt parking lot milling, choosing a contractor with the right mix of expertise, modern equipment, and local insight can significantly influence the outcome. Taking the time to research and compare local providers pays dividends in ensuring that the final result meets both performance and budgetary expectations.
Future Trends and Advancements
As the field of asphalt maintenance continues to evolve, the future of milling in Madison Heights holds promising advancements that are expected to reshape the way commercial properties approach surface rehabilitation. Technological innovations and environmental considerations are at the forefront, driving improvements in efficiency, accuracy, and sustainability. One of the most noteworthy trends is the increasing adoption of sophisticated milling machines that integrate real-time data analytics. These machines are capable of providing instant feedback on surface conditions and milling depth, allowing operators to adjust operations dynamically and ensure superior outcomes. Such advancements not only maximize the longevity of the milled surface but also optimize the use of materials, contributing to cost savings and environmental stewardship.
There is also a growing emphasis on the utilization of sustainable practices within the milling industry. As recycling technologies improve, the reclaimed asphalt from milling projects is finding increasing application in new surface overlays. This circular approach to material use demonstrates a strong commitment to reducing waste and lowering carbon emissions. Innovations in asphalt cold milling continue to refine the process by offering more energy-efficient alternatives that minimize environmental impact. Commercial property owners in Madison Heights have shown considerable interest in these green initiatives, recognizing that sustainable practices can lead to both regulatory advantages and improved public perception.
Another area where significant progress is anticipated is digital integration. Advances in software technology are enabling the use of sophisticated mapping, modeling, and project management tools that streamline the entire milling process. Contractors are now able to simulate projects in a virtual environment before actual implementation, identifying potential challenges ahead of time. This preemptive strategy not only saves time and materials but also reduces the margin of error during on-site operations. The ability to digitally manage projects fosters a higher level of precision, ensuring that each milling project meets exacting standards of quality and durability.
In tandem with these technological trends, there is a growing market demand for specialized services tailored to unique commercial needs. Milling contractors are expanding their capabilities, offering bespoke solutions that address specific issues such as impaired drainage, compromised structural integrity, and unique traffic load challenges. This trend is driven by the increasing sophistication of commercial projects that require a nuanced understanding of pavement behavior and the integration of multiple layers of surface protection.
As the industry moves forward, the collaboration between local businesses, property owners, and milling service providers is expected to deepen. With advancements in machinery, software, and sustainable practices, the role of milling in preserving and enhancing commercial properties will become even more critical. Forward-thinking companies that invest in these innovative practices will likely see substantial returns in the form of longer-lasting surfaces, reduced maintenance costs, and improved operational efficiency. This proactive attitude towards modernization is crucial as Madison Heights continues to grow and commercial properties face ever-evolving demands.
Reflecting on these trends, it is evident that the future of milling is not just about repairing old surfaces; it represents a comprehensive approach to infrastructure maintenance that aligns with progressive economic and environmental goals. By embracing advancements in milling technology and sustainable practices, commercial properties can position themselves at the forefront of modern urban development. For property owners considering future-proofing their investments, the evolving landscape of milling offers both promising innovations and renewed confidence in the durability of their surfaces.
In the competitive commercial environment of Madison Heights, staying ahead means continuously adapting to technological trends while upholding high standards of quality. This forward-thinking approach will undoubtedly shape the way cities, businesses, and communities manage their infrastructure, ensuring that the milling process remains a vital component in the ongoing journey towards safer, more sustainable, and economically viable commercial properties.
As the comprehensive guide to milling in Madison Heights illustrates, the milling process offers significant advantages that extend well beyond surface repair. Through careful planning, technical expertise, and the effective application of advanced machinery, milling transforms aging surfaces into robust, enduring foundations for new asphalt overlays and other maintenance projects. The process not only contributes to aesthetic improvements, safety enhancements, and long-term durability but also aligns with broader environmental goals. By integrating practices such as asphalt cold milling and the use of recycled materials, local contractors are demonstrating that effective pavement rehabilitation can coexist with sustainability.
The real-world applications of milling—from parking lot renewal to thoroughfares—are testament to its role as a critical tool for property managers and municipal planners alike. Commercial properties in Madison Heights that have embraced regular milling as part of their maintenance schedule experience fewer unexpected failures, reduced repair costs, and an overall boost in the longevity of their surfaces. The success stories of local developments highlight how customized milling solutions, backed by advanced technology and meticulous project management, are creating safer, more attractive, and more efficient urban spaces.
Furthermore, the economics of milling are undeniable, providing substantial cost savings over traditional methods while also ensuring environmental benefits and compliance with modern urban standards. The combination of recycling, specialized techniques, and technology-driven operations makes milling a smart, forward-thinking investment for commercial properties. By choosing experienced and reputable contractors—such as the widely recognized D&J Contracting—property owners in Madison Heights can secure high-quality results that not only meet but exceed industry expectations.
In essence, milling stands as a transformative process that bridges the gap between aging infrastructure and a vibrant, sustainable future. The intricate blend of technical process details, financial prudence, and ecological responsiveness makes it an invaluable strategy for any commercial property manager committed to long-term excellence. As urban areas continue to expand and the demands on commercial surfaces increase, the insights offered in this guide serve as a powerful reminder of why milling is an essential component in the ongoing evolution of urban maintenance.
For those looking to secure the future value and appeal of their commercial properties in Madison Heights, the journey begins with understanding the milling process. It is an investment in durability, safety, and improved operational efficiency. Through careful planning, embracing new technologies, and engaging with knowledgeable contractors, businesses can ensure that their surfaces remain a testament to quality and longevity. As milling continues to evolve, so too will the strategies that keep our urban landscapes resilient and dynamic, paving the way for brighter, more sustainable futures.
Milling Gallery
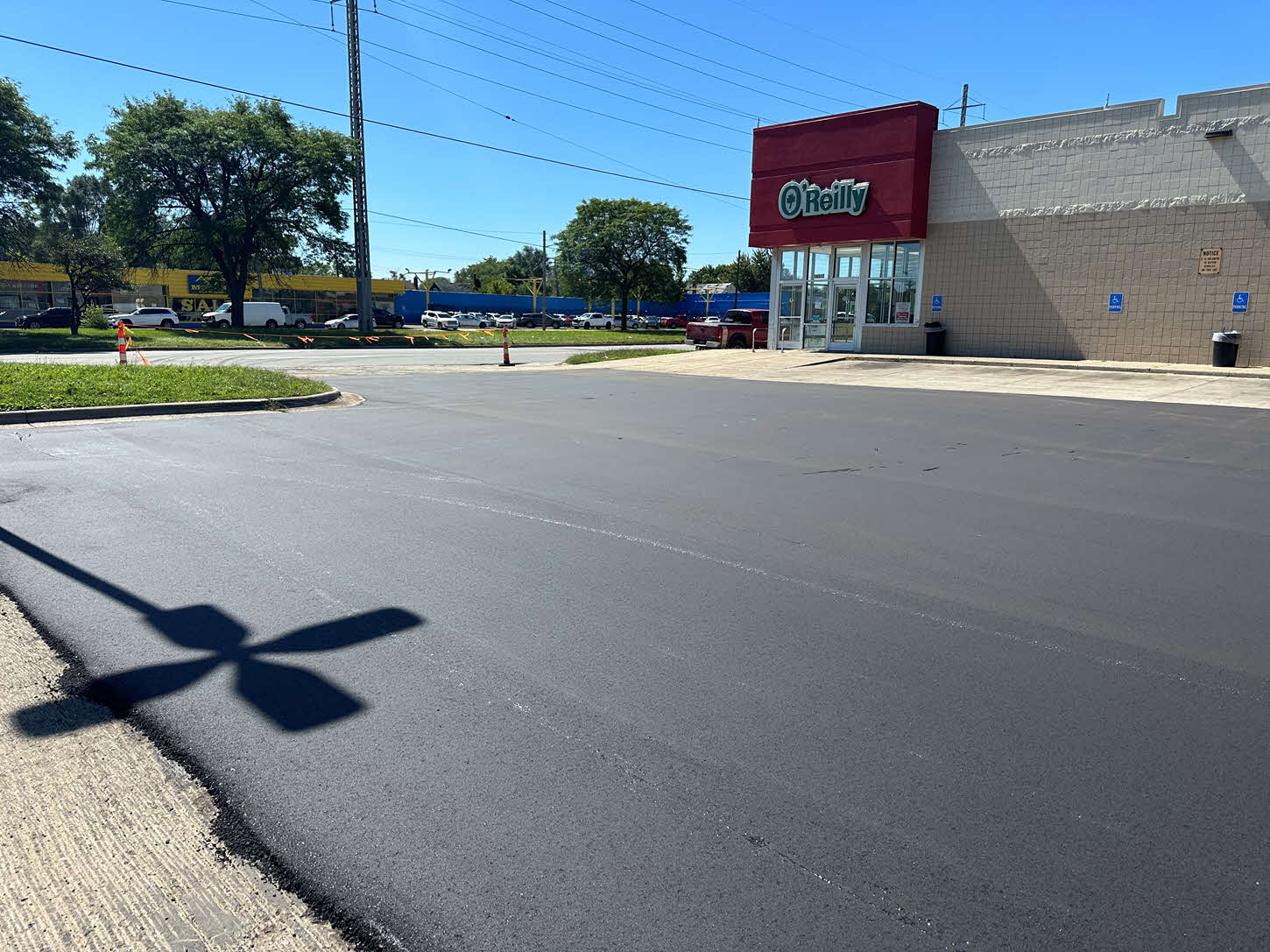
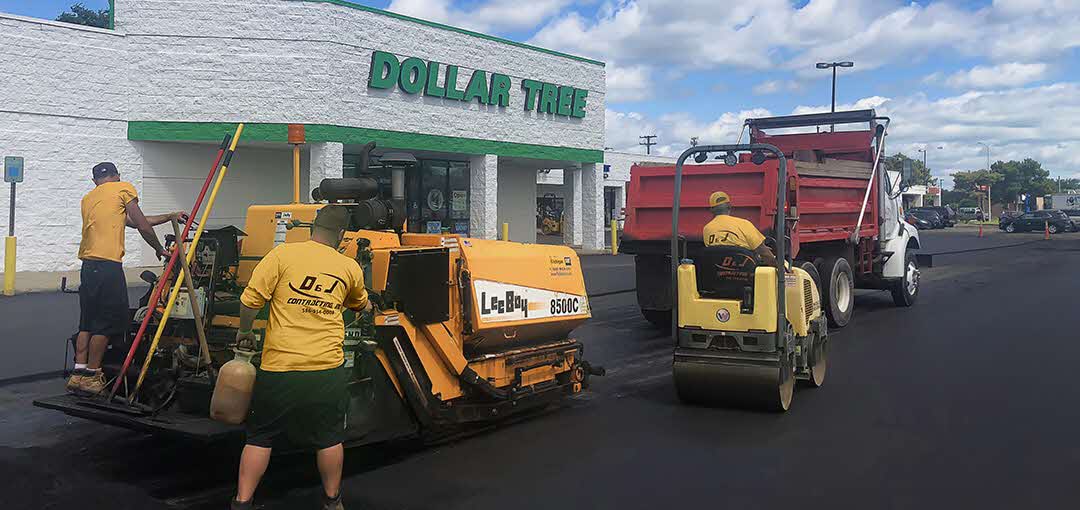
Call Us Today to receive your Free Quote for
Milling in Madison Heights
Serving: Madison Heights, Michigan
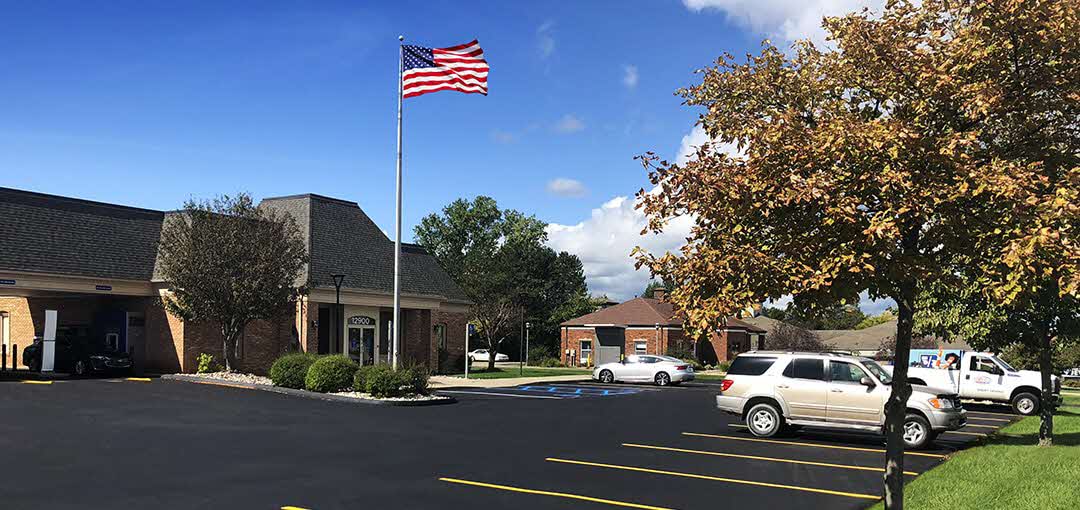
About Madison Heights, Michigan
Originally part of Royal Oak Township, Madison Heights incorporated as a city by popular vote on January 17, 1955, and chartered on December 6 of that same year, becoming the tenth city government in southern Oakland County. At that time, the 7.2 square miles (18.6 km) city was one of the largest suburban communities in the Metro Detroit area. The first city hall was at 26305 John R Road, the former township offices. On April 5, 1963, a new municipal building was dedicated which is on the present location at 300 West Thirteen Mile Road. The city lies in the Interstate 696 (I-696) and I-75 corridor and is served by two primary school districts, Lamphere and Madison, as well as a full-service municipal government.
According to the United States Census Bureau, the city has a total area of 7.09 square miles (18.36 km), all land.
Although 91% of the buildings in Madison Heights are single-family homes or condominiums (approximately 9,800 residential property owners), 60% of the tax base is fueled by light industrial or commercial property. The city has 15 voting precincts, totaling more than 21,000 registered voters.
Madison Heights shares borders with Troy to the north, Royal Oak to the west, Hazel Park to the south, and Warren to the east. The eastern border of Madison Heights (Dequindre Road) is also the border between Oakland and Macomb counties.
There are more than 112 miles (180 km) of road within Madison Heights, of which the city maintains 105 miles (169 km), 95 miles (153 km) for snow removal, sweeping, and patching. Interstate 75 passes north to south on the west side of the city, and Interstate 696 is the major feature of its southern border. The junction of these two highways is shared with Royal Oak and Hazel Park on the southwest corner of Madison Heights.
Census | Pop. | Note | %± |
---|---|---|---|
1960 | 33,343 | — | |
1970 | 38,599 | 15.8% | |
1980 | 35,375 | −8.4% | |
1990 | 31,296 | −11.5% | |
2000 | 31,101 | −0.6% | |
2010 | 29,694 | −4.5% | |
2020 | 28,468 | −4.1% | |
U.S. Decennial Census |
As of the 2020 United States census of 2020, there were 28,468 people and 13,487 households in the city. The population per square mile is 4,017.5.
The racial makeup of the city was 80.4% White, 7.8% African American, 0.2% Native American, 7.2% Asian, 0.1% Pacific Islander, 3.6% from two or more races. Hispanic or Latino residents of any race were 2.0% of the population.
There were 13,487 households, of which 14.7% spoke a language other than English at home. People under 65 years of age with a disability accounted for 11.1% of the city’s population, and 11.7% of the city’s population was living below the federal poverty line. Households without a broadband internet subscriptions made up 11.9% of the community.
16% of residents were under the age of 18; and 16.3% were 65 years of age or older. The gender makeup of the city was 49.4% male and 50.6% female.
As of the census of 2010, there were 29,694 people, 12,712 households, and 7,543 families residing in the city. The population density was 4,188.2 inhabitants per square mile (1,617.1/km). There were 13,685 housing units at an average density of 1,930.2 per square mile (745.3/km). The racial makeup of the city was 83.9% White, 6.4% African American, 0.5% Native American, 5.8% Asian, 0.1% Pacific Islander, 0.7% from other races, and 2.7% from two or more races. Hispanic or Latino residents of any race were 2.5% of the population.
There were 12,712 households, of which 27.5% had children under the age of 18 living with them, 41.0% were married couples living together, 12.9% had a female householder with no husband present, 5.4% had a male householder with no wife present, and 40.7% were non-families. 34.1% of all households were made up of individuals, and 11.8% had someone living alone who was 65 years of age or older. The average household size was 2.32 and the average family size was 3.02.
The median age in the city was 38.3 years. 20.4% of residents were under the age of 18; 8.7% were between the ages of 18 and 24; 30.4% were from 25 to 44; 26.6% were from 45 to 64; and 13.9% were 65 years of age or older. The gender makeup of the city was 49.1% male and 50.9% female.
As of the 2000 United States census, there were 31,101 people, 13,299 households, and 8,005 families residing in the city. The population density was 4,341.3 inhabitants per square mile (1,676.2/km). There were 13,623 housing units at an average density of 1,901.6 per square mile (734.2/km). The city’s racial makeup was 89.60% White, 1.82% African American, 0.44% Native American, 4.97% Asian, 0.03% Pacific Islander, 0.46% from other races, and 2.68% from two or more races. Hispanic or Latino residents of any race were 1.61% of the population.
There were 13,299 households, of which 26.9% had children under the age of 18 living with them, 45.2% were married couples living together, 10.5% had a female householder with no husband present, and 39.8% were non-families. 33.8% of all households were made up of individuals, and 12.3% had someone living alone who was 65 years of age or older. The average household size was 2.33 and the average family size was 3.02.
In the city, 22.1% of the population was under the age of 18, 8.1% was from 18 to 24, 35.4% from 25 to 44, 20.2% from 45 to 64, and 14.2% was 65 years of age or older. The median age was 36 years. For every 100 females, there were 95.8 males. For every 100 females age 18 and over, there were 92.9 males.
The city’s median household income was $42,326, and the median family income was $51,364. Males had a median income of $41,478 versus $29,345 for females. The city’s per capita income was $21,429. About 7.0% of families and 8.9% of the population were below the poverty line, including 10.8% of those under age 18 and 13.0% of those age 65 or over.
In 2008, 1.9% of the Madison Heights population were of Vietnamese descent. 168 Asian Mart, a 38,000-square-foot (3,500 m) supermarket, is the largest Asian supermarket in southeast Michigan, and one of the largest in the state. The Chinese Cultural Center is in Madison Heights.
The mayor of Madison Heights is Roslyn Grafstein, who was appointed as Mayor in August 2020 to fill a vacant seat.
District | Representative | Party | Since |
---|---|---|---|
11th | Haley Stevens | Democratic | 2023 |
District | Senator | Party | Since |
---|---|---|---|
3rd | Stephanie Chang | Democratic | 2023 |
District | Representative | Party | Since |
---|---|---|---|
8th | Mike McFall | Democratic | 2023 |
57th | Thomas Kuhn | Republican | 2023 |
District | Commissioner | Party | Since |
---|---|---|---|
3 | Ann Erickson Gault | Democratic | 2023 |
Madison District Public Schools and Lamphere Public Schools have public schools serving Madison Heights.
Bishop Foley Catholic High School is a private school.
Four Corners Montessori Academy is a public charter school.
Call Us Today to receive your Free Quote for
Milling in Madison Heights
Related Services in Madison Heights, Michigan
We Serve Businesses In The Following Zip Codes:
48007, 48015, 48021, 48026, 48035, 48036, 48038, 48042, 48043, 48044, 48045, 48046, 48047, 48048, 48050, 48051, 48066, 48071, 48080, 48081, 48082, 48083, 48084, 48085, 48088, 48089, 48090, 48091, 48092, 48093, 48098, 48099, 48225, 48230, 48236, 48310, 48311, 48312, 48313, 48314, 48315, 48316, 48317, 48318, 48397